
Responsibility
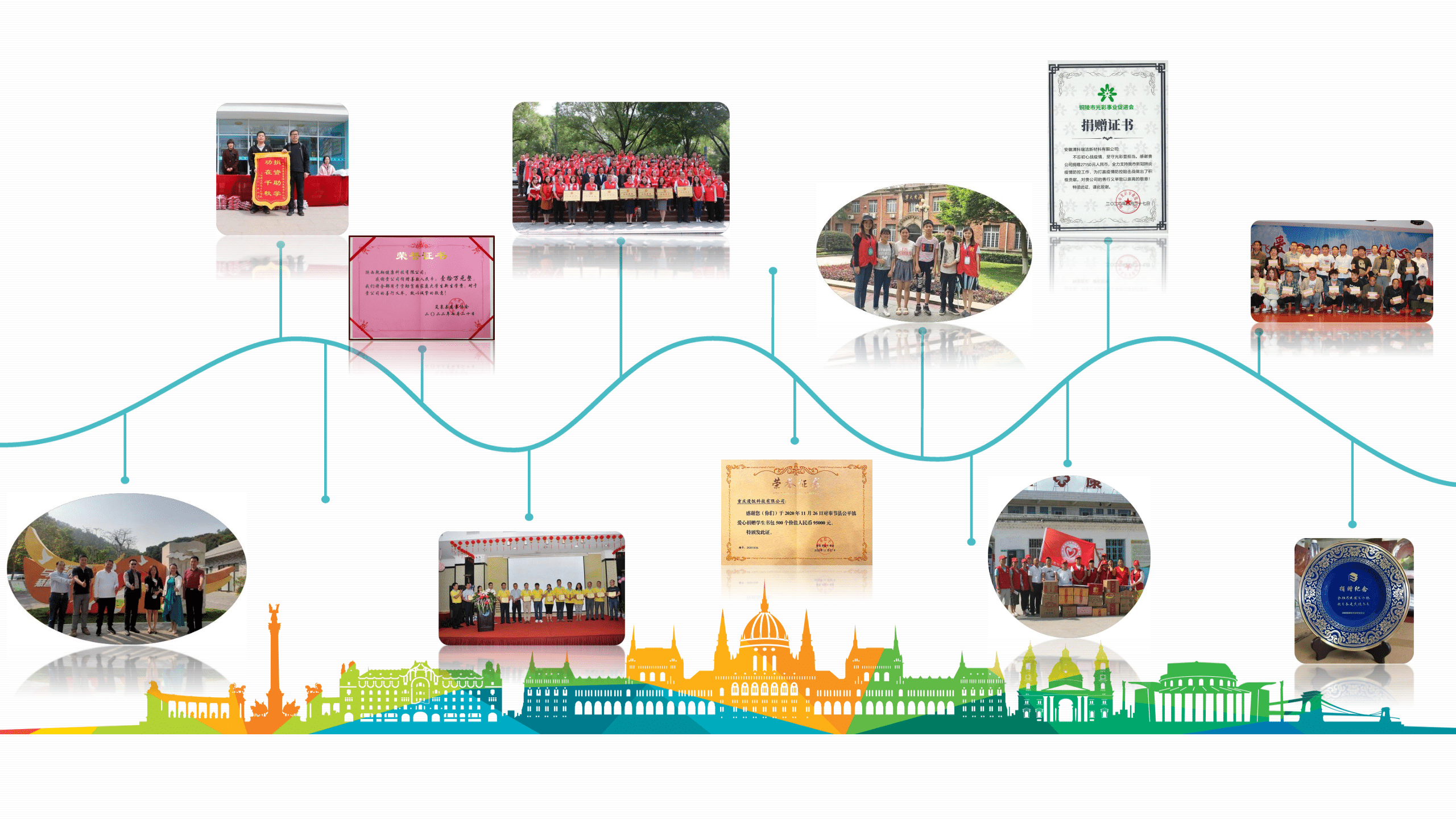
Conflict-Free Minerals Statement
Dear Customer:
PEAK is committed to providing our customers with products that are conflict-free and we are committed to investigating the source of such metals in our supply chain to ensure that Au,Ta, W,Co, Sn and other such metals are not mined by anarcho-corps or illegal groups from mines in the DRC and surrounding countries or obtained through illegal smuggling. PEAK is committed to establishing a complete conflict minerals policy, management system and investigation framework that is consistent with relevant laws and regulations, requiring suppliers to conduct source tracing and responsible mineral due diligence on minerals used in products they purchase, and to share due diligence information with customers to ensure that supply chain policies are consistent with the requirements of the guidelines and to gradually improve supply chain transparency and supply chain governance. If conflict minerals are used, they will be immediately reported to our customers and corresponding supporting materials and subsequent rectification plans will be provided according to customer requirements.
DRC and its neighboring countries include: Democratic Republic of Congo (DRC), Republic of Congo (ROC), Central African Republic (CAR), South Sudan (SOUTH SUDAN), Zambia (ZAMBIA), Angola (ANGOLA), Rwanda (RWANDA), Uganda (UGANDA), Burundi (BURUND), Tanzania ( TANZANIA).
Supplier Code of Conduct
PEAK requires all of its suppliers to conduct their business in a socially and ethically responsible manner, including providing a safe working environment, ensuring that its workers are treated with respect and dignity, and that the business operates in an environmentally responsible and ethical manner. All suppliers and their contractors shall comply with the provisions of EICC and SA8000 as well as this Code, which briefly describes our requirements for its suppliers in the areas of labor, health and safety, environment, ethics and management systems.
1、Labor
Our suppliers are committed to upholding the human rights of our employees and treating them with dignity and respect in accordance with the relevant guidelines of EICC and SA8000. This applies to all employees, including temporary workers, immigrants, apprentices, contract workers, direct employees and any other types of employees.
The labor standards are
1.1 Free Choice Of Employment
No forced, bonded (including debt bondage) labor, involuntary prison labor, slavery, or human trafficking shall be employed. Suppliers shall enter into written employment contracts with their employees that contain a statement of statutory terms and conditions, as required by law. All work must be voluntary and employees shall have the right to resign at any time in accordance with the law. Suppliers and agents shall not retain or otherwise destroy, conceal, confiscate, or deny employees access to their identity or immigration documents, such as government-issued identification, passports, or work permits, unless required by law to retain work permits.
1.2 Young Employees
Child labor shall not be used at any stage of manufacturing. A “child” is any person under the age of 15, below the age of completion of compulsory education, or below the national/regional minimum age for employment, whichever is highest. Support the use of legal workplace apprenticeship programs that comply with all laws and regulations. Employees under the age of 18 (young employees) are not permitted to perform work that may endanger health or safety, including night and overtime work.
1.3 Working Hours
Weekly working hours must not exceed the maximum limit set by local law. Also, unless in an emergency or unusual situation, the work week may not exceed 60 hours, including overtime. Employees shall have at least one day off every seven days.
1.4 Salary and Benefits
Wage Compensation. Overtime work on regular workdays, overtime work on rest days, and overtime work on legal holidays must be paid in accordance with local legal requirements. Compensation and benefits are provided to employees fairly, and the components of wages and benefits are clearly stated and must not be less than the minimum wage in the region.
1.5 Humane Treatment
Employees shall not be subjected to harsh inhumane treatment such as sexual harassment, sexual abuse, corporal punishment, mental or physical coercion, or verbal abuse; nor shall they be threatened with such acts.
1.6 Non-discrimination
The Company will not engage in or support any act of discrimination based on race, social class, national origin, religion, disability, gender, sexual orientation, union membership or political affiliation in matters of hiring, compensation, training opportunities, promotion, job placement (including overtime), or termination of employment based on the individual employee’s ability and the needs of the job.
1.7 Freedom of Association
As required by local law, suppliers shall respect the right of all employees to freely associate and join unions, bargain collectively and participate in peaceful assemblies, and the right of employees not to participate in such activities. Employees or their representatives shall be able to communicate and share suggestions and opinions openly with management regarding the work environment and management practices without fear of discrimination, retaliation, threats or harassment.
- Health and Safety
In addition to minimizing work-related injuries and illnesses, establishing a safe and healthy work environment can improve the quality of products and services, facilitate production, improve employee retention and boost employee morale. Suppliers should also understand that ongoing employee engagement and education is critical to identifying and addressing health and safety issues in the workplace.
The health and safety standards are
2.1 Occupational Safety
Potential safety hazards (e.g., electrical and other energy, fire, vehicle, and fall hazards) that employees may encounter should be controlled through proper design, engineering and management controls, preventive maintenance and safe work processes, and ongoing safety training. If hazards cannot be effectively controlled by the above means, employees should be provided with appropriate, well-maintained personal protective equipment and educational materials about the risks that may result from the hazards described above. Employees should be encouraged to raise safety concerns.
2.2 Emergency Preparedness
Emergency situations and emergencies should be identified and evaluated and their impact minimized through the implementation of emergency response programs and procedures, including: emergency reporting, employee notification and evacuation procedures, employee training and drills, appropriate fire detection and suppression equipment, adequate egress facilities, and recovery plans. Such plans and procedures should minimize hazards to persons, the environment, and property.
2.3 Workplace Injuries and Illnesses
Procedures and systems should be in place to prevent, manage, track, and report occupational injuries and illnesses, including provisions to: encourage employees to report them; classify and record cases of occupational injuries and illnesses; provide necessary medical care; investigate cases and take corrective action to eliminate the effects; and assist employees in returning to work.
2.4 Industrial Hygiene
The effects of chemical, biological and physical agents on employees should be identified, evaluated and controlled. Engineering or management techniques must be used to control overexposure to hazards. When these methods cannot be used to effectively control hazards, the health of employees must be protected through appropriate personal protective equipment programs.
2.5 Intense Physical Work
The effects on employees of performing physically demanding work, including manual handling of materials and repetitive heavy lifting, prolonged standing, and highly repetitive or forceful assembly work, should be identified, evaluated, and controlled.
2.6 Machine Guarding
Safety hazard assessments shall be performed on production equipment and other machinery. Physical guards, interlocking devices, and barriers shall be provided and properly maintained for machinery that may result in employee injury.
2.7 Public Health, Catering and Accommodation
Employees shall be provided with clean restroom facilities, potable water, and clean food preparation, storage and dining facilities. Employee quarters provided by suppliers or labor agencies shall be maintained in a clean and safe manner with appropriate emergency exits, hot water for bathing, adequate heating and ventilation, and reasonable access to private space.
2.8 Health and Safety Communication
Suppliers shall provide employees with appropriate workplace health and safety training taught in the employee’s primary language. Health and safety related information shall be clearly posted in the workplace.
- Environment
Manufacturing operations shall be conducted in a manner that minimizes adverse impacts on communities, the environment, and natural resources while protecting public health and safety.
The environmental standards are
3.1 Environmental Permitting and Reporting
All required environmental permits (e.g., emission monitoring), approval instruments, and registration certificates shall be obtained, maintained, and updated, and their operation and reporting requirements shall be complied with.
3.2 Environmental Pollution and Resource Conservation
All types of resource depletion and pollution (including water and energy) shall be reduced and eliminated at the source or through practices (e.g., improved production, maintenance, and facility processes, material replacement, resource conservation, material recycling and reuse).
3.3 Hazardous Substances
Chemical substances and other materials that pose a hazard when released into the environment shall be identified and controlled, and their safe handling, transportation, storage, use, recycling or reuse, and disposal shall be ensured.
3.4 Wastewater and Solid Waste
Suppliers shall take a systematic approach to identifying, managing, reducing and responsibly disposing of or recycling solid waste (non-hazardous substances). Wastewater generated from operational activities, industrial processes and sanitary facilities needs to be identified, monitored, controlled and treated for its nature as required prior to discharge or disposal. In addition, measures should be taken to reduce wastewater generation. Suppliers shall routinely monitor the performance of their wastewater treatment systems.
3.5 Exhaust Emissions
Emissions of volatile organic chemicals, aerosols, corrosives, dust, ozone-depleting chemicals and combustion byproducts generated during operations shall be identified, routinely monitored, controlled and treated as required prior to emission. Suppliers shall routinely monitor the performance of their exhaust emission control systems.
3.6 Material Restrictions
Suppliers shall comply with all applicable laws and regulations and customer requirements that prohibit or restrict the use of specific substances in products and manufacturing processes (including labeling regarding recycling and disposal).
3.7 Stormwater Management
Suppliers shall take a systematic approach to preventing pollution from storm water runoff. Suppliers shall prevent illegal discharges and spills of substances into drains.
3.8 Energy Consumption and Greenhouse Gas Emissions
Energy consumption and greenhouse gas emissions shall be tracked and recorded at the workplace level or at the enterprise level. Suppliers shall seek cost-effective ways to improve energy efficiency and minimize energy consumption and greenhouse gas emissions.
- Ethics
To fulfill their social responsibility, suppliers and agents shall follow standard ethical requirements, including
4.1 Business Integrity
The highest standards of integrity shall be followed in all business interactions. Suppliers shall adopt a zero tolerance policy prohibiting any form of bribery, corruption, extortion and misappropriation of public funds. All business transactions shall ensure transparency and shall be accurately reflected in supplier business accounts and records. Oversight and enhanced procedures shall be implemented to ensure compliance with anti-corruption related laws and regulations.
4.2 No Improper Benefits
No bribes or other forms of improper or improper benefits shall be promised, offered, granted, given or accepted. The prohibition covers promising, offering, granting, giving or receiving anything of value, either directly or indirectly through a third party, for the purpose of obtaining or retaining business, assigning business to anyone, or otherwise obtaining an improper advantage.
4.3 Intellectual Property
Intellectual property rights shall be respected; transfer of technical or experiential knowledge shall be done in a manner that protects intellectual property rights; and the security of customer information shall be protected.
4.4 Fair Dealing, Advertising and Competition
Standards of fair dealing, advertising and competition shall be upheld. The security of customer information must be protected in an appropriate manner.
4.5 Anti-money Laundering, Convenient Payment Attention Obligations
The supplier shall strictly comply with the relevant provisions of China’s Anti-Money Laundering Law and prevent criminal activities of money laundering. The supplier shall establish a customer identification system and, when establishing business relationships or conducting transactions with customers, shall require the transaction recipient to provide and verify his or her identity information data. Keep the identity information and real transaction records of the transaction subjects and give active and reasonable cooperation when financial institutions or law enforcement agencies conduct investigations of suspicious transactions or large transactions. Use convenient payments with caution to avoid facilitating and assisting criminal money laundering activities.
4.6 Identity Protection and Non-Retaliation Policy
Procedures should be in place to protect suppliers and employee whistleblowers and to ensure the confidentiality and anonymity of their identities, unless expressly prohibited by law.
4.7 Responsible Minerals Procurement
Suppliers shall have policies in place to provide reasonable assurance that none of the tantalum, tin, tungsten, and gold contained in their manufactured products will directly or indirectly finance or benefit armed groups that commit serious human rights abuses in the Democratic Republic of the Congo or neighboring countries/areas (conflict zones). Suppliers shall conduct due diligence on the source and chain of custody of these minerals and provide the customer with the due diligence measures taken upon request.
- Management Systems
Suppliers shall adopt or establish a management system whose scope is relevant to the content of this Code.
The management system shall contain the following elements:
5.1 Privacy
Suppliers shall be committed to protecting a reasonable expectation of privacy for the personal information of all persons involved in the business, including suppliers, customers, consumers and employees. Suppliers shall comply with privacy and information security laws and regulatory requirements when collecting, storing, processing, transmitting and sharing personal information.
5.2 Corporate Commitment
A corporate social and environmental responsibility policy statement that articulates the supplier’s commitment to compliance and continuous improvement and is signed by management, issued in local languages and posted in the workplace.
5.3 Management Accountability and Responsibility
Suppliers shall clearly assign responsibility for ensuring the implementation of the management system and related programs to senior management and company representatives. Senior management shall periodically review the status of the management system.
5.4 Training
A program to train managers and employees to achieve the supplier’s policies, procedures and improvement objectives and to comply with applicable legal and regulatory requirements.
5.5 Corrective Action Procedures
Procedures used to promptly correct deficiencies identified during internal or external assessments, inspections, investigations, and audits.
5.6 Documentation and Records
Documents and records are created and maintained to ensure compliance with regulations and confidentiality provisions related to company requirements and protection of privacy.
5.7 Supplier Responsibilities
Procedures for communicating Code requirements to own suppliers and monitoring compliance.
Who is PEAK?
Founded in 2007, PEAK Co.,Ltd is an electronic solutions company offering 1-64 layers PCB fabrication, assembly, testing & validation of rigid, rigid-flex, HDI, high frequency, high speed, metal core, IC substrate, substrate-like and other special PCB. Our modern 54,000 square foot manufacturing facility allows us to provide all rigid & rigid-flex services under one roof and offer quick-turn capabilities. PEAK has a professional reputation for developing high-performance solutions for technically advanced OEM’s in a variety of markets including aerospace and defense, medical, computer, communication, server, semiconductor IC, automotives, industrial control, optoelectronics, LED and others.
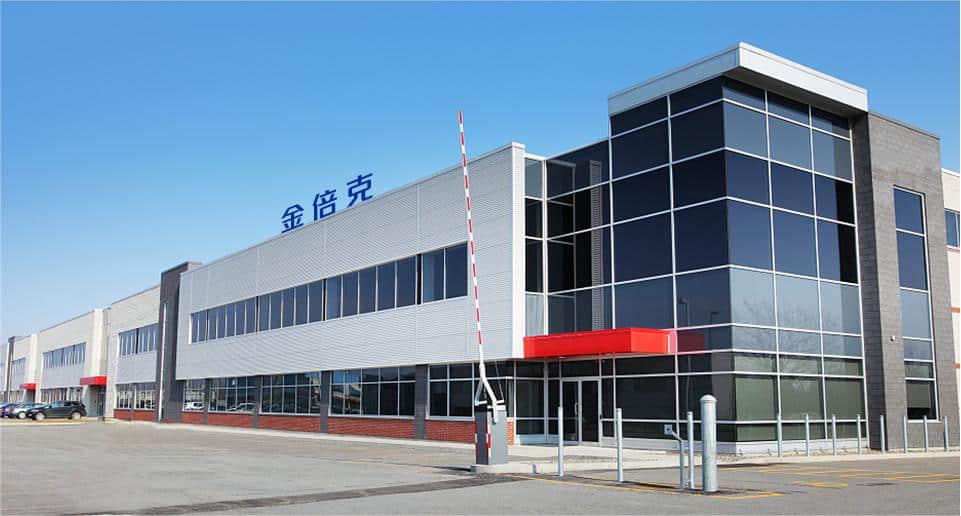

Ability to Handle Complex Jobs
All Rigid & Rigid-Flex Services Under One Roof
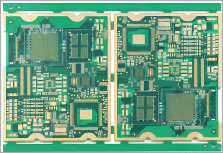
Regular PCB
Up to 64 Layers; FR4 TG135/TG150/TG170; Halogen Free/CTI≥600; Aspect Ratio (Finish Hole) 28:1; Sample Expedited 8 Hours(1-2Layer);
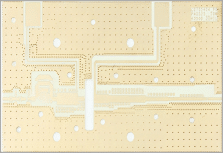
Metal Core PCB
Thermal Conductivity 1-398W/m.K; Aluminum/Copper AC 500-4000V; Post-bonding/Pre-bonding; Sweat-Soldering/Conductive Adhesive; Press-Fit/Embedded Coin(I, T U);

HDI PCB
Blind/Buried/Hybrid Via; 5+N(N+M)+5 Structure; Trace Width/Spacing 1.6/1.6mil; Laser Hole Size(mm)≥0.075; High Density Interconnector;
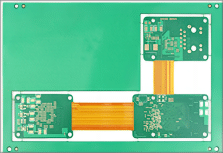
Rigid-Flex PCB
2-24 Layers; Book/Air-gap/Fly-tail; Unsymmetrical/Semi-Flex; Width of Flexible Zone 3mm(min); Dimension Accuracy ±0.05mm(min);
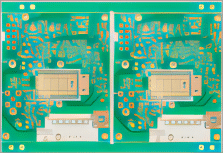
High Frequency PCB
More than 85+ Types; Rogers/Arlon/Taconic/Isola/ Nelco/F4B Serices,etc; Materials can be Specified; Impedance Tolerance ±5%(min);
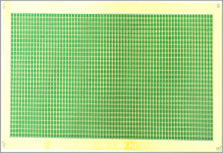
Substrate PCB
CSP/FC-CSP/SIP/FC-BGA/WB-CSP; FR4/BT/High-Speed Material; Trace Width/Space 12/12μm; SM Registration:±20μm; Strict SM Flatness Control ≤5μm;
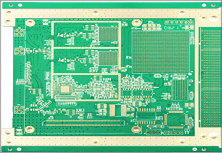
High Speed PCB
Panasonic Megtron4/6/7; TU-872SLK/Isola-FR408HR,etc; Impedance Tolerance ±5%(min); Dimension Accuracy ±0.02mm(min); Line Width/Space Accuracy ±5%;
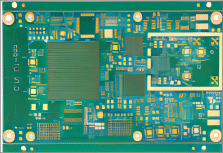
Specialty PCB
Ceramic/Glass Material; Hybrid Material Lamination; Buried Capacitance/Resistance; PTH/NPTH Step Slots; Uneven/Segmented/Step Gold Finger;